2019 Zalkin Capper 10 Head Rotary Capping Machine Type CA10/480 - TPV3
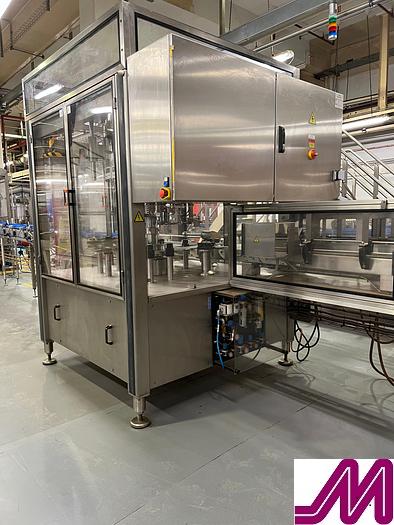
Specifications
Manufacturer | Zalkin Capper |
Model | 10 Head Rotary Capping Machine Type CA10/480 - TPV3 |
Year | 2019 |
Description
GENERAL DESCRIPTION
Pitch circle diameter: 480 - Pitch: 150.80
Conditioning environment: food
Product to be capped:
Direction of the feed: right/left (counter clockwise)
Layout: N°1232379
Material: made of stainless steel 304 L on guard turret, bottle carrier plate, shaft and starwheel
bearing, head-carrier, lower sleeve, central shaft, upper frame, top plate, collars and spacers
Maximum output: 19800 Bph
Cam: with sealing profile – pick and place - stroke 100 – Material: Polyamide
Heads slides: New Gen with no greasing
Pick and place: cap transfer by starwheel with pegs (8 position)
Electrical height adjustment gauge
Greasing: centralized ,Vogel stainless steel
Pneumatic components: FESTO
GUARD
Protective guard (Polycarbonate with stainless steel frame) with 2 front doors and 2 back doors.
ELECTRICITY
Power supply : Three phases network 415 V - 50 Hz
Control circuit voltage: 24 Vdc
TSEIN Control box with « L » shape, on infeed side
Dimensions: 800 x 1650 x 400 mm
Operator interface on the side of the control box, front of the machine
Machine speed controlled by ALLEN BRADLEY frequency inverter. Signal to drive the inverter
comes from the Ethernet network
Ejection conveyor’s speed driven by ALLEN BRADLEY frequency inverter. Signal to drive the
inverter comes from the Ethernet network
ALLEN BRADLEY security sensor on the guard’s doors
ALLEN BRADLEY programmable security relays to drive emergency stops and security sensors
Caps control in cap chute with SICK photocell:
- Detection at low point: machine stops when cap chute is empty
Automatic mode driven by SICK photocells in upstream (lack of bottles) and downstream (bottle
jam) to allow the machine to automatically start/stop according to the quantity of bottles on the
conveyor
Complete management of the machine with ALLEN BRADLEY PLC CompactLogix and ALLEN
BRADLEY HMI PanelView +7 (10 inches).
Fallen bottles detection on infeed conveyor. Machine will stop in case of defect
Caps presence on bottles checked with SICK photocell and angled caps checked with SICK optic
fiber.
Ejection of non-compliant bottles, machine stop after X consecutive defects (can be programmed on
HMI) and operator called with red beacon
5 colors PATLITE beacon to show the machine’s state
FESTO solenoid valve for air cut on machine and cap sorter
Caps presence on bottles checked with SICK photocell and angled caps checked with SICK optic
fiber.
Ejection of non-compliant bottles, machine stop after X consecutive defects (can be programmed on
HMI) and operator called with red beacon
5 colors PATLITE beacon to show the machine’s state
FESTO solenoid valve for air cut on machine and cap sorter
HEADS
10 sealing heads type TPV3 :
10 lower parts with quick release system set for caps 100g Lipstick 800 Line - purple
10 lower parts with quick release system set for caps 165g Lipstick 800 Line - yellow
EQUIPMENTS
• Glass jar 100gr Ø69*69 x 149.8 mm - purple
• Glass jar 165gr Ø85.7*85.7 x 150 mm – yellow
Bottles gripping device by synchro power belt
Equipments marking via engraving and color
1 infeed scroll for 100gr format
1 infeed scroll for 165gr format
1 guiding rail in front of scroll
Set of transfer equipments for bottles including infeed starwheel, central starwheel, outfeed starwheel, front and back centrale guide rails (PEHD-MSOFT white):
Bottle body equipments for jar 100gr / purple color plug - RAL 4008
Bottle body equipments for jar 165gr / yellow color plug – RAL1018
CAP FEEDING DEVICE
• Plastic cap (to seal) Ø68.7*68.7 x h 50 mm
• Plastic cap (to seal) Ø84.3*84.3 x h 63 mm
7.1 Cap chute
For caps 100 gr ø 68.7*68.7 x h 50 mm
1 cap chute in “J” shape to connect to customers’ conveyor + 1 flat articulation + 1 caps dispenser with quick release